1. Data Acquisition Setup
- For the fixed condition, the yaw platter supports a 4-m strongback,
rigid post, load cell, fixed mount, and ship model and restrains all
translations and rotations of the model.
- Sinkage and trim is set at the fixed mount for a few tests at Fr = 0.28.
- For the free condition, the yaw platter supports the loadcell, 1.5-m
strongback, three balances that enable pitch, heave, and roll (fixed or free)
motions and restrain surge, sway, yaw motions.
- Roll motion is enabled or disabled with spherical or one-degree-of-freedom
connection bearings, respectively, at the fore and aft balances.
- In both fixed and free cases, model 5512 is mounted on the tank centerline at
its design waterline (except for fixed tests with sinkage and trim) and either
towed from z = 0.01m (fixed) or z = 0.0m (free).
- Force and moment data cables are run to six onboard amplifiers.
- For measuring sway position, a linear potentiometer is fixed to the carriage
frame and linked to the sway box with wire loop, two pulley wheels, and
bracket.
- For measuring yaw position, a rotational potentiometer is fixed inside the sway
box and linked to the yaw platter with a wire loop.
- Data lines connect both potentiometers to amplifiers aboard the drive carriage.
- The Krypton camera module is mounted backward-facing from the rear underside of
the drive carriage to gain an unobstructed view of the LED target.
- The target is mounted near the bow and over the models centerline such that the
LED’s face the camera module.
- The targets position places it within zone #1 of the measurement volume.
- Axial (DxLCG = -593 mm) and vertical (DzLCG
= 213 mm) measurements from the target center to the LCG are made to
enable the Krypton software to shift local measurements at the targets origin to
the LCG of model 5512.
- This shift is setup in software and occurs synchronously as data is acquired.
- 6DOF ascii motion data is reported from the camera controller at 40 Hz.
- Analog data lines from the loadcell, motion tracker, PMM potentiometers, and
carriage speed circuit are run to the drive carriage to an onboard 16-channel AD
card and PC.
2. Data Acquisition Procedures
- First, at-rest reference voltages are measured for all
instruments.
- Then, the PMM is activated and ten seconds elapse to allow enough
time for the motion to reach a steady rate.
- When this condition occurs, the carriage is started and
accelerates through 10 m to a constant speed.
- Data acquisition commences after traveling another 10 m which
allows the unsteady free surface to develop and reach a state where it is not in
transition.
- Data acquisition occurs at 100 Hz / channel for 30, 20, 10
seconds, respectively, for cases where Fr = 0.138, 0.28, 0.41, respectively.
- For static drift tests, the PMM remains inactive during the
carriage run, however, all other procedures above are followed.
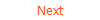
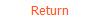